News - Press Release
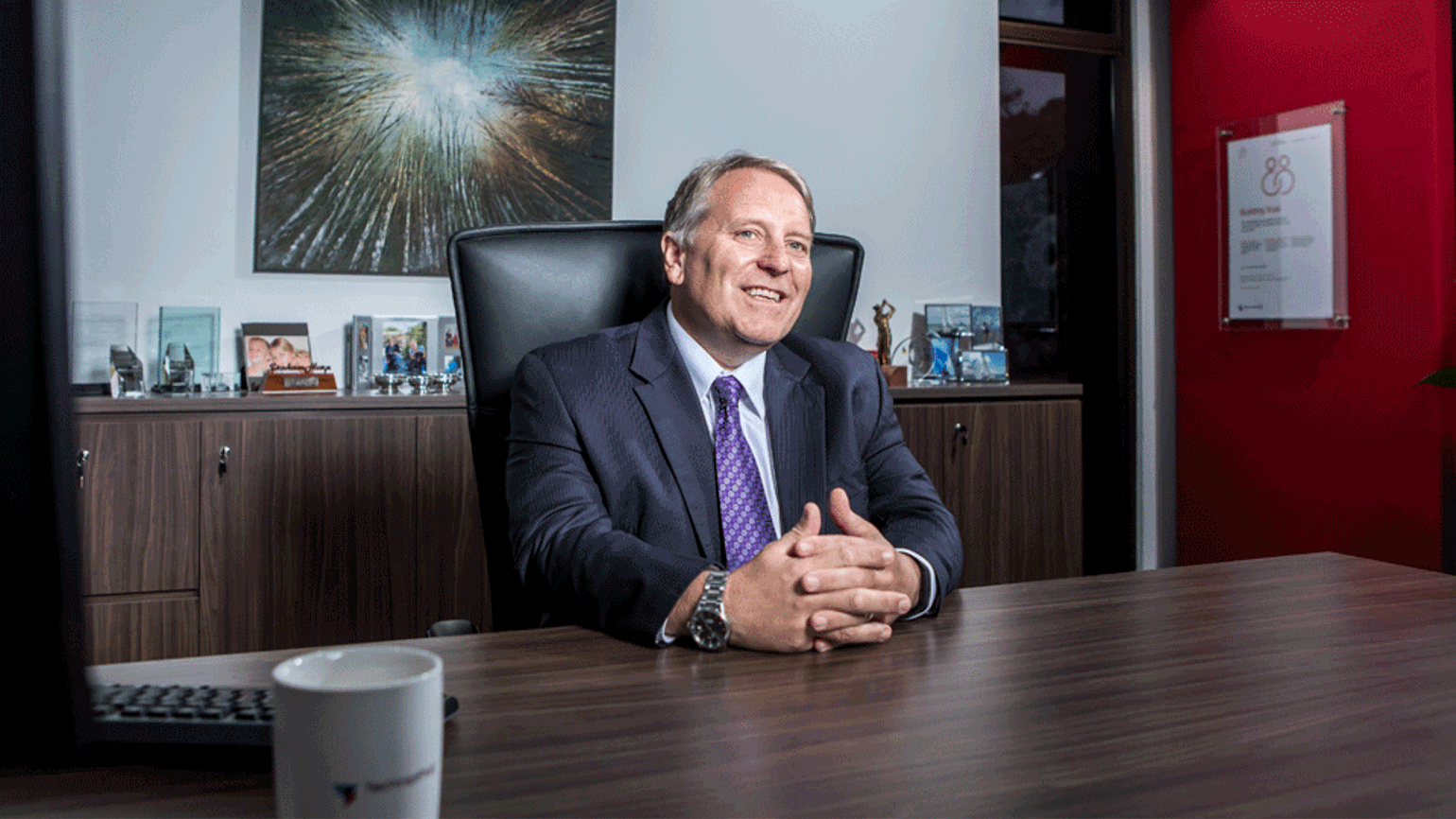
iProduction™ is TechnipFMC’s integrated solution for shale oil production – designed, built and installed by our Surface business segment.
The flexible, modular system combines cutting-edge separation technology with actionable data to lower customers’ cost, time to first production, and green house gas (GHG) emissions.
Graham Horn, Senior Vice President Surface Product Management, explains how iProduction™ “joins the dots between wellhead and the export pipeline”.
-
What are the benefits of iProduction™ as an integrated solution?
-
Graham Horn (GH): “This is one of the first integrated solutions we are putting into the field as Surface Technologies. We have integrated separation technology, oil treatment technology, metering, remote monitoring and automation, to provide a smart solution.
“This approach is redefining what we do in Surface. We have exploited lessons learned offshore to develop an integrated offering. Pre-engineered modular solutions are installed in the field and start producing oil more quickly than bespoke facilities. The automation and integrated sensors provide the customer with actionable data, through a single universal program, drastically reducing the operating costs and increasing efficiency by reducing manpower required in the field.”
-
What makes iProduction™ different to other shale oil production systems?
-
GH: “The technology in the separators and the intermediate heating system really sets iProduction™ apart, as well as the digital twin using i2 Integrated Intelligence.
“Our High Pressure Separator (HPS), where we remove most of the gases from the crude, can process three times the volume of a standard HPS. Another key differentiator is the Advanced Oil Separation (AOS) System, where we have integrated the Low Pressure Separator with the Intermediate Heating System. That takes a lot of parts out of the production facility, helping us reduce the footprint and capital costs. And thanks to our digital solution, it can be tightly controlled remotely, which allows our customers to hit their oil stabilization target in the separator thereby removing the need for storage vessels which are normally used and which are the source of much vapour release. We’re saving on GHG emissions, footprint, capital costs and operating costs.”
-
How valuable is the data iProduction™ feeds back using i2 Integrated Intelligence?
-
GH: “In general, the more accurate data we can provide the customer on what is coming out of the field, the better the customer can alter settings to get the best flow of oil or gas. i2 was designed from day one to feed into our UCOS data lake to provide the customer with data in an actionable form.
“Data is leveraged to determine when maintenance has to take place, instead of routine quarterly or yearly inspections. The system determines when an intervention needs to occur and flags it up months in advance. The customer can gather together all the maintenance that needs to be done then take care of it at the same time, reducing downtime and increasing efficiency. Some routine maintenance, such as jetting the sand which gathers in the HPS, can even be performed without a shutdown, instead of the typical 12 to 24 hours of downtime.
“The whole system is self-regulating. It’s checking on itself continuously to make sure that it is functioning the way it should, as well as validating the production data. When you become dependent on data, you need to know the data is reliable and the sensors providing the data are working as expected.”
-
What kind of savings can a customer expect?
-
GH: “The capital costs are 33 percent lower because of the 40 percent smaller footprint and reduced number of elements. Because we build off-site and install at the location, we need less manpower in the field and the client gets to first oil 30 percent faster.
“And the reduced need for manpower means lower running costs and reduced exposure to risk, too.”
-
What is the environmental impact of iProduction™?
-
GH: “Emissions are cut. A standard production set up producing 15,000 barrels a day would have 2,300 tonnes of CO2 equivalent in emissions each year. With iProduction™, that’s reduced to under 1,000 tonnes, and we are continuing to look at further enhancements to bring this down further.
“One source of GHG savings is the reduction in methane emissions. Methane regularly escapes from storage vessels, but here it all goes to export – and methane is one of the worst greenhouse gases. iProduction™ is a closed circuit. There is nowhere that gas can get out. The methane that would ordinarily leech out in storage is extracted by our more efficient AOS System. Because of that, we’ve been able to remove one of the flares, which would typically connect to storage. The other flare is really only used at start-up or in an emergency.
“We are committed to designing integrated systems that will not only reduce total costs for our customers, but also reduce and one day eliminate emissions.”
More news
-
News | May 06, 2025
TechnipFMC Advances Hybrid Flexible Pipe Technology Innovation in Collaboration with Petrobras
-
News | March 18, 2024
Inside HISEP® – How TechnipFMC is taking dense gas separation and storage fully subsea
-
News | October 19, 2023
TechnipFMC wins NOIA ESG Excellence award