News - Press Release
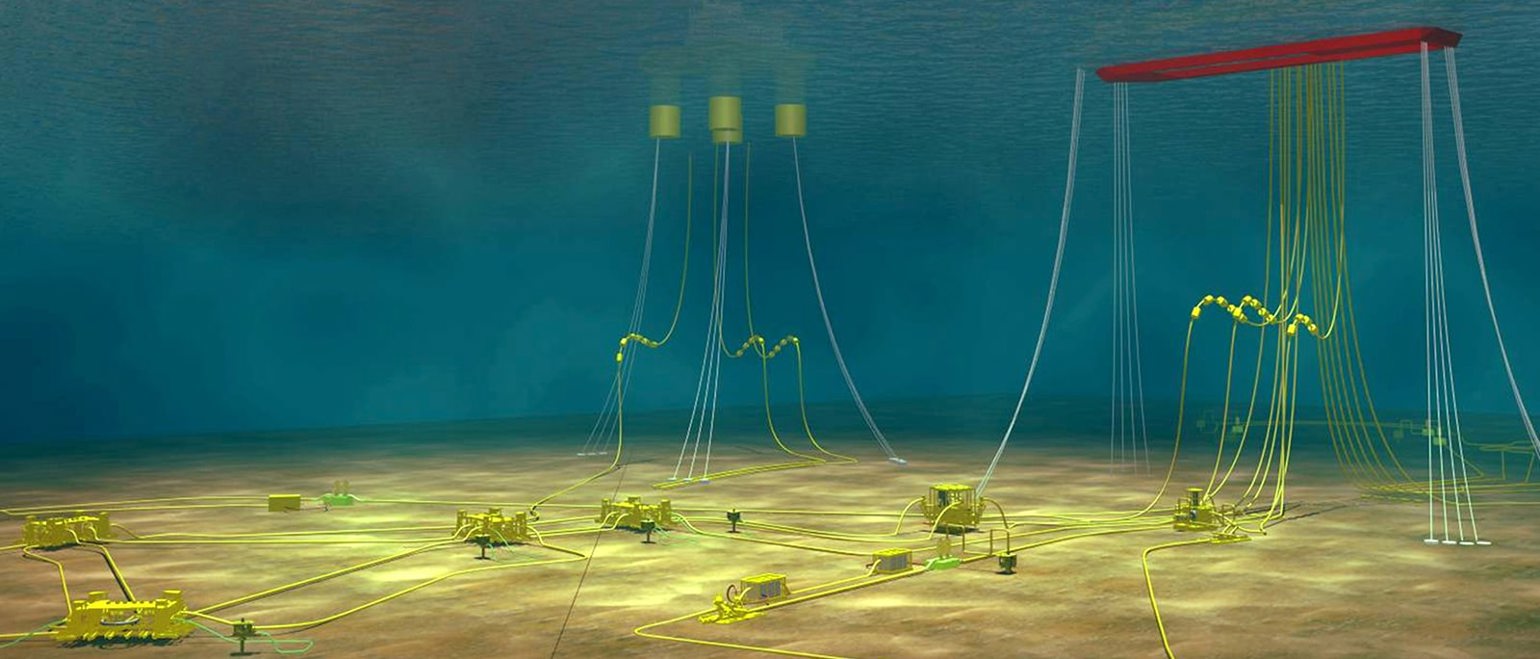
In the current business environment, there is an even stronger focus on cost reduction. This has also put monitoring systems in the spotlight, as they can bring cost-effective solutions to complete offshore field.
Recording data to provide sustainable products and solutions
Monitoring can be divided into two categories: monitoring of an asset (e.g. measuring bearing temperatures or vibrations of a pump to check for degradation) and monitoring of production (e.g. process flows parameters to ensure efficient handling of products). Where monitoring starts to get really valuable to an operator is when the information provided is used in a smart way.
Predictive Maintenance of an equipment item, as opposed to Periodic Maintenance performed based on running hours recommendations from equipment suppliers, uses real-time data from a monitoring system to determine when maintenance is actually required. This can lead to extended times between inspections and thereby reduces the overall maintenance cost. However to gain the most advantage from Predictive Maintenance the multiplicity of information received from the monitoring systems must be analyzed in a smart fashion, to provide good advice to the operator.
The need for monitoring solutions for offshore mooring systems and subsea risers has been a niche market targeted by Cybernetix, a TechnipFMC entity. Increasingly, operators are understanding the value of monitoring systems for such equipment. Critical components that previously did not have any form of monitoring to predict imminent or actual failure are now available. The value of these monitoring systems is that they can monitor the fatiguing stress to which a critical component is subjected and determine the remaining life of that component.
Systems to monitor component stresses are ideally installed at the start of an installation’s life so that fatigue can be monitored from Day 1. Retrofittable systems however can also provide useful information about an existing facility and still allow an assessment of useful residual life. Different deployment methods address both cases.
There is a great benefit to the operator in extending the life of an existing facility: to provide continuing production or utility support functions and offset final decommissioning. It is in this area that the direct relationship between monitoring systems and cost saving is easiest to demonstrate.
Installing monitoring systems from Day 1 enables an operator to follow the overall behavior of components and reduce operational uncertainties during the life of an installation. The information gained can then be used to improve the components' design (e.g. by reducing safety coefficients) and improve the design software (e.g. by checking or calibrating for more accurate predictions of loadings) which will ultimately lead to lower CAPEX.
Some examples of how Cybernetix monitoring solutions can help reduce costs
The Anchor Leg Load Monitoring System is a monitoring solution for mooring lines. Different technologies can be used within the system depending on its objectives. For breakage or overstress alarms, top angles are measured by inclinometers. For stress cycling monitoring, load cells or vibrating wires (ex-tension/compression measurements) measure parameters that enable tension calculations. By following angles or tension variations, operators have access to the actual status of the mooring lines and get valuable information to decide on maintenance or repair before a failure occurs or for making life extension decisions.
The Riser Tension Monitoring System, based on vibrating wire technology, continuously calculates the tension of a rigid riser from extension/compression measurements, allowing long-term remaining life assessment. As for flexible pipes, a better knowledge of operational behavior also helps to improve design coefficients.
The Morphopipe System is dedicated to flexible pipe risers. It is installed at a top location on the riser under the stiffener, where dynamic loads are very stringent due to environmental constraints. An array of sensors, embedded in a dedicated layer, measure the curvatures experienced by the riser. Monitoring curvature cycling loads, correlated with environment data measurements, gives access to the remaining lifetime of the equipment when compared to design calculations. In addition, the follow-up of actual dynamic cycles over the flexible riser lifetime allows re-assessment of the safety coefficients used during design phases.
Conclusion
All the above systems, by monitoring subsea key component conditions, lead to operational risk reduction and operating cost saving. They also help to reduce design and construction uncertainties and offshore manning for inspections, which translates again into cost reductions whilst maintaining high levels of safety.
More news
-
News | May 06, 2025
TechnipFMC Advances Hybrid Flexible Pipe Technology Innovation in Collaboration with Petrobras
-
News | March 18, 2024
Inside HISEP® – How TechnipFMC is taking dense gas separation and storage fully subsea
-
News | October 19, 2023
TechnipFMC wins NOIA ESG Excellence award